2.基本的压缩机知识
压缩空气作为工厂内仅仅次于电能的第二大动力消耗能源,是工厂生产运行的基本保障。因此作为压缩空气生产的机械设备维护运行人员其岗位职责相当重要。
但实际上,大多工厂空压机的操作运行人员并非全部来自于这个专业或长期从事这项工作,往往是临时的或者只会开机关机,对于基本的压缩机知识一无所知。




低压压缩机——排气压力小于1.0MPa
中压压缩机——排气压力1.0~10MPa
高压压缩机——排气压力10~100MPa
超高压压缩机——排气压力大于100MPa


V代表压缩机形式,3—排气量即产气量,20—代表排气压力最高可达20MPa。


空气的组成:氮气78%,氧气21%,氩气0.93%,二氧化碳0.03%,氖气0.0018%,其他惰性气体、水分和尘埃、二氧化硫、一氧化碳等有毒气体。
压缩空气是指具有一定的压力,并对空气中尘埃、水分进行过处理的可再生能源。压力、流量、温度是压缩空气的三个基本指标。干空气的分子量为28.96,在0℃、760mmHg时的密度为1.293g/m3。


压力表、温度计、尘埃粒子计数器、露点仪。


1.露点:一定压力下饱和空气在保持水蒸气分压力不变情况下降低温度使之达到饱和状态。(即结露凝结水析出),此时的温度叫露点温度。
2.压缩比:压缩机排气压力和进气的绝对压力之比。
3.绝对压力是考虑到与完全真空或绝对零值相比,我们所居住的环境大气具有0.1MPa的绝对压力。
4.大气压力:衡量大气的压力。绝对压力=压力表显示压力+大气压力。
5.饱和空气:当没有再多的水气能容纳在空气中时,就产生了空气的饱和,任何加压和降温均会导致冷凝水的析出。
6.常压空气:规定压力为0.1MPa,温度为20℃、相对湿度为36%状态下的空气为常态空气。
7.标准状态:规定吸入压力为0.1MPa,温度为0℃状态下的提供给用户系统的空气。


在维修保养时应做到“三必须”:任务前必须明确分工,有计划有责任人,填写认真;进行拆卸、安装工作时机件必须放在档油盘或堑板上,不得落地放置或随意乱放;工作完毕后必须对工作场所进行彻底打扫和清理,恢复场地原貌。
1.机组运行1000~1500Hrs维护保养内容:
(1)清洗空气过滤器。
(2)检查各级排污阀的开启情况,如管路不通、及时疏通管道。
(3)检查各仪表使用是否完好。
2.机组运行2000~2500Hrs维护保养内容:
(4)更换受损的空气过滤器滤芯。
(5)检查压力和温度读数;
(6)检查机组可能存在的空气或油泄露部分维护。
(7)在水冷却器上检查可能存在的水泄露,
(8)清洗冷却器,清洗冷干机的冷凝器。
(9)更换油和油过滤器,当油分离器上压降超过1bar时,更换油分离器。检查油水分离器及排污管路畅通情况,及时疏通管路。
(10)检查电器自动控制部分,如各级压力的超高、超低报警情况。
(11)检查电控柜内接线柱紧固情况、安全接地及安全防护装置可靠情况。
(12)检查无热再生干燥塔、粗过滤、除油过滤器情况。
3.机组运行3500~4000Hrs维护保养内容:
(13)压缩机部分:
a)更换油过滤器滤芯,更换润滑油。
b)检查清洗单向断油阀弹簧柱塞,必要更换。
c)清洗恒温阀,如有必要适当可更换。
d)检查磨损件的配合间隙,并作好记录,为大修提供原始记录。
e)清洗油冷却器及后冷却器水套内水垢。
(14)操作监控系统
a)各级压力表、安全阀的灵敏度,校检。
b)各管路阀门灵敏度。
c)发现确已损坏更换之。
(15)冷却水系统
a)清洗冷却水箱内水垢及污物。
b)清洗水泵进口过滤网内污物。
c)检查冷却塔内污物;检查风机旋转情况、检查布水器旋转情况,更换或添加润滑脂。


空压站点检表(附表1)
空压运行记录(附表2)
空压站机组保养工作内容(附表3)
3.为什么变频空压机保养要贵很多?
近年来,在大家的共同努力之下,用户对变频空压机认可度越来越高,其销量也逐年上涨。现在的空压机代理商如果不提变频与节能,都不好意思说自己是卖空压机的了。可以说,空压机行业已进入变频与节能时代。
相对工频空压机来说,变频空压机的好处很多,这也是近几年越来越多的用户接受变频空压机的主要原因。比如,变频空压机恒压运行,没有了空载,能效大大提升,对于绝大多数空压机用户而言,变频空压机的确节能。变频空压机还能满足用户生产旺季与淡季用气量波动的需求,另外,变频空压机软启动也能降低用户电网负荷。
空压机厂家、空压机代理商大力主推变频、节能空压机,用户欣然接受变频空压机,说明从生产者、销售者到用户,大家节能意识都很强了,这是利国利民的好现象。但是,不少空压机代理商以及绝大多数用户,只清楚变频空压机节能,并没有意识到变频空压机与工频空压机因为设计与运行等技术的改变,变频空压机对维护、保养的要求远远高于工频空压机,还是按工频空压机的要求维护、保养变频空压机,导致变频空压机故障率较高,节能效果也大打折扣,这与大家追求变频空压机稳定、节能的初衷是相违背的。在此举一个很相近的生活案例:涡轮增压与自然吸气的汽车,其维护、保养方面是有区别的,涡轮增压的汽车维护、保养要求远远高于自然吸气的汽车,汽车尚且如此,何况与工频空压机差别更大的变频空压机呢?
图文无关
为了便于大家容易理解为什么变频空压机保养要贵很多,本文以简单易懂的方式叙述,希望对于行业同仁有所帮助!
变频空压机对润滑油品质的要求远远高于工频空压机,不能按工频空压机的使用标准选用润滑油。原因如下:
1.变频空压机低频时容易积水,对润滑油的耐水性要求远远高于工频空压机;
2.工频空压机有加载与卸载之分,变频空压机一直都处于加载状态,相同的运行时间,变频空压机加载时间远远高于工频空压机的加载时间,变频空压机运行2000小时,相当于工频空压机运行2500-3000小时,甚至更多;
3.变频空压机运行温度整体来说,要比工频空压机高一些,因此对润滑油耐温性要求比工频空压机要高得多。简单一点说,相同型号的空压机,变频空压机对润滑油品质的要求,比工频空压机要高1-2个档次。因此,变频空压机一定要选用比工频空压机高1-2个档次的优质润滑油。
变频空压机因为频率与压力变化,排气量也会跟着变化,油分桶内的油雾含量也跟着在变化,排气量与油雾含量的变化,会导致油分阻力大小跟着变化。比如,一台变频空压机压力维持在6公斤满速运行时,其排气量是远远大于6至8公斤加载、卸载的工频空压机。排气量大了,油分桶内的油雾含量也会加大,压缩空气通过油分时的流速也会加快,容易油耗大、内压高,高流速对油分的损坏速度也会加大。同理,变频空压机一直处于加载状态,不像工频空压机有加载、卸载之分,变频空压机加载时间远远高于工频空压机加载时间;选择变频空压机油分时,是必须要考虑这些因素的。
变频空压机容易积水,水分较多时容易损坏油分的滤纸,导致油分容易油耗大或者跑油。比如:55kW工频空压机用DB2132油分很稳定,但完全相同的油分装在55kW变频空压机上使用,稳定性就不高。有一部分机器1000多到2000小时左右就会油耗大或者跑油。由此可见,变频空压机对油分的要求是远远高于工频空压机的,选择变频空压机油分时,是必须要考虑这些因素的。
大家细细回想一下,最近5年以来,很多油分的稳定性是不是感觉不如5年前了?主要原因是近几年以来变频空压机越来越多,变频空压机对油分的要求远远高于工频空压机。因此,变频空压机一定要选用符合变频空压机使用要求的优质油分。
何为优质空滤?单一追求过滤精度高,或者单一追求不容易堵塞的空滤,都不是优质空滤。只有同时具备过滤精度高、吸气阻力小两项指标的空滤,才算得上是优质空滤。
变频空压机为什么要使用优质空滤?因为无论是空压机厂家、空压机代理商,还是空压机用户,大家的初衷都是希望变频空压机稳定、节能。优质空滤吸气阻力小可以扩展运行能效,优质空滤过滤精度高,对润滑油保护较好,对油分中、后期压差保护比较好,可以更好的扩展空压机运行能效。变频空压机满速运行时,排气量会大很多,优质空滤由于过滤精度高,拦截粉尘效果极佳,大大保护了油分的有效过滤面积,对油分的稳定性起到非常大的辅助作用。因此,变频空压机一定要选用优质空滤,如果一味以低价迎合用户,按工频空压机的标准使用空滤,既是对自己不负责任,更是对用户的不负责任。
何为优质油滤?过滤精度中等,阻力小,容尘量大、外壳耐腐蚀强等等,综合在一起才称得上优质油滤。为什么变频空压机对油滤的要求远远高于工频空压机?因为变频空压机低频时容易积水,对油滤滤纸的抗水能力、滤纸阻力小的要求远远高于工频空压机,对油滤外壳抗腐蚀能力要求远远高于工频空压机。变频空压机实际加载时间远远高于工频空压机,因此对滤纸的抗老化能力和滤纸的容尘量的要求要远远高于工频空压机。变频机对油滤的过滤效果、油滤阻力小的要求同样要远远高于工频空压机,因此变频空压机一定要选用符合变频空压机使用要求的优质油滤。
为什么会有很大一部分用户热衷于接受变频空压机低价保养、维护?因为用户不是专家,用户不懂其中的利害关系,低价保养、维护带来的危害用户短时间内看不到,贪图便宜的心理占上风是人之常情,我们应该以自己的专业知识去引导用户,与用户达到双赢,而不是投其所好,以低价竞争去误导用户,最终损人不利己。
虽然让用户认识到低价保养、维护带来的危害很大,其见效相对比较慢,只有吃过几次亏,才会认识到低价保养得不偿失,但我们依然必须长期坚持去引导。用户选择低价保养、维护的主要原因是为了省钱,笔者建议大家先从省钱的角度着手引导用户,效果会更佳。而对比保养周期中、后期的运行电流,是最直接有效的方法。笔者相信,除了少数有个性的用户以外,大多数用户是不愿意接受得不偿失的低价维护、保养的。
图文无关
我们不要只是抱怨用户喜欢便宜,要从自身找原因,单纯追求便宜的用户毕竟只是极少数的,大多数追求便宜的用户,缘于我们努力不够,不能有效的引导用户,没有让用户意识到变频空压机正确的保养、维护才是最便宜的。当初变频空压机也只有少量用户选用,在大家长期坚持引导之下,用户逐渐清楚了变频空压机的优点,采购成本高一些的变频空压机算起总账来,反而比工频空压机更便宜,进而更多用户欣然接受变频空压机。在变频空压机的保养、维护方面,上述道理同样适用。
4.变频空压机频繁加卸载常见原因和解决方法
变频压缩机和工频相比,使用时用气量可调,启动平滑,供气压力相比工频会稳定些,但有时候也会像工频压缩机一样出现频繁加卸载的情况。
针对这个现象简单分析发现,频繁加卸载的情形通常为以下几种情况:
原因1、供气压力和卸载压力设定的值过于接近
当压缩机达到供气压力时,若用气量突然减小,变频器来不及控制电机减速,就会造成产气量过大,从而造成卸载的情况。
解决方法:把供气压力和卸载压力之间的差值设的大些,通常差值≥0.05MPa
原因2、当电机恒定频率运行时,面板显示压力上下波动
解决方法:换一个压力传感器。
原因3、用户用气量不稳定
用户用气量不稳定,会突然增加减少很大的用气量。这时候供气压力就会变动,变频器控制电机变频改变输出气量来维持供气压力稳定。但是电机的转速变化都是有速度的,当这个速度跟不上用气端的用气变化速度时就会造成机器的压力波动,然后可能会出现加卸载的情况。
解决方法:(1)用户不要突然使用多台用气设备,可以一台一台的开启用气的设备。(2)将变频器的变频速度调快,让输出气量的改变速度增快来适应用气量的变化。(3)用大容量的储气罐来缓冲。
原因4、用户用气量过小
通常永磁变频压缩机的变频范围为30%~100%,异步变频压缩机的变频范围为50%~100%。当用户用气量小于压缩机下限输出气量时,气量达到设定的供气压力以后,这时候变频器会控制电机降频至下限频率以下限输出气量来输出压缩气体,但是因为用气量太小,供气压力就会继续升高,直到卸载压力,机器卸载。然后供气压力下降,压力下降至低于加载压力时,机器重新加载。
对这种情况做一个分析。就是当用气量很小机器卸载时,该不该让压缩机进入休眠状态,或者说卸载多少时间以后再进入休眠状态。当机器卸载时,用气端也是在用气的,但是一旦压缩机进入休眠状态以后,压缩机不在产生用气,这时候供气压力会下降,下降至加载压力后,机器加载。
这里会出现一种情况,就是当机器从休眠状态开始重新启动时,用户的压力还在下降,很可能会出现供气压力低于加载压力,甚至远低于加载压力的情况,造成供气压力过低或者供气压力波动特别巨大的情形。所以建议卸载后进入休眠状态的时间不宜过短。
5.空压机的加载与卸载
压机供气压力在达到Pmax(卸载压力)时,空压机停止产气,但仍然在空转运行的工作状态,即不打气,但电机还在转,电表还在走,你还在交电费。一般状况下,卸载时的耗电量一般为加载时的45%,耗电浪费严重,建议空压机加载率(加载时间/总运行时间)在85%以下时,可选择变频空压机来避免卸载,减少电能浪费。
6.关于空压机工艺运行情况的分析及探讨
1 引言
涩宁兰全线共有5座压气站,其中4个压气站每个站设置有3台SA-30型空气压缩机,另外一个压气站设置有2台功率较大的SA-37A型空气压缩机。本文分析的是安装在乌兰压气站的SA-30型空压机。
2 SA-30型空压机
SA-30型空压机属于螺杆式空压机,双轴容积式回转型。进气口位于机撬上端,排气口位于下部,一对主、副转子,水平且平行安装,主转子有5个齿,副转子有6个齿,两者相互啮合。整个空压机系统主要由空气过滤器、进气阀、油气桶、油细分离器、安全阀、泄放电磁阀、除尘过滤器、再生塔等部件组成。
目前,这种型号的空压机由安装在空压机房的联控柜中控的运行模式控制。下面是乌兰压气站空压机设置的一些常见参数的范围。
联控柜:压力上限(停空压机):0.92 MPa,压力下限(启空压机):0.70 MPa;1#空压机:加载压力:0.70 MPa,卸载压力:1.0 MPa;2#空压机:加载压力:0.70 MPa,卸载压力:1.0 MPa;3#空压机:加载压力:0.70 MPa,卸载压力:1.0 MPa。
3 问题
对乌兰压气站的参数进行趋势分析,发现仪表气总管网压力持续保持在0.9 MPa达5 h,现场查看发现3#空压机运行且处于加载状态。这里需要指出的是由于涩宁兰复线的建设,空压机在原来两台的基础之上新建了3#空压机,所运行的工艺流程也是在原来的基础之上改进的,3#空压机相对于1#、2#有一定的差别。
3台空压机分别运行时的总管网压力如图1所示。
从历史趋势中可以看出,在升压阶段,3台空压机都升到0.9 MPa,由于卸载压力均设置在1.0 MPa,因此3台机组继续加载运行。
不同之处在于1#、2#空压机在后续加载运行中总管网压力升至0.92 MPa,达到了联控柜的停机压力值,联控柜发出停机命令,空压机进入空载运行,至总管网压力降至0.7 MPa后继续加载运行,形成一个加载-空载的运行循环直至联控柜切换机组指令。而3#机组则一直加载运行直至联控柜切换机组指令。
针对这种情况,会产生一定的能耗损失,空压机空载运行时的能耗约为加载运行时的三分之一。以3台机组平均时长运行为例,3#空压机比1#和2#空压机每天多耗电30 kWX2 hX2/3=40 kW·h。
4 原因分析
经查看3台空压机的功率等参数一致,排除了3台机组性能不一致的可能。
分析发现总管网压力探头位于1#和2#空压机出口汇管处,3#空压机则直接连在储气罐上,故初步判断是由于管网拓扑和压力传感器位置(如图2所示),导致3#空压机在加载运行时无法将管网压力提升至联控柜设定的停机值,导致一直加载运行[5]。
5 解决办法
将3#空压机的卸载压力设定为0.90 MPa,使其在出口压力达到0.90 MPa时候自动进入空载运行模式,实现加载-空载的运行循环,有效的避免了3#空压机一直处于加载运行的工作状态。
6 运行模式探讨
针对以上工艺运行情况分析来看,空气压缩机长时间的运行对达到节能降耗的目的是不利的,另外由于索拉机组对于隔离气的使用需求较大,也致使了涩宁兰沿线增压站内的空压机基本处于24 h连续运转的状态。为此,根据各种不同的工艺运行情况来适当的调节空压机的运行参数,达到节能降耗的目的。
对乌兰压气站内使用仪表气的设备进行调查,如表1所示:
6.1 工况1:压缩机全部运行或者热备用空压机连续24 h不间断运行,总管网压力上下限和空压机空车过久的时间设置(如乌兰站的总管网压力上限0.90 MPa,下限0.70 MPa,空压机卸载压力1.0 MPa,加载压力0.7 MPa,空车过久
35 min) 应保持空压机处于加载-空载的运行循环,也就是空车过久设置时间即空压机最长空载运行时间(35 min) 跃总管网压力下降所需时间(约30 min),避免反复启机,如图3所示。
6.2 工况2:有1台压缩机处于冷备用状态(全部断电)
压缩机冷备时可以将其隔离气的手阀关闭,空压机每天约运行22 h (乌兰实测值)每天可节能30 kW伊2h=60 kW·h。
通过图4可以注意到总管网压力下降所需时间为40 min左右,存在的问题是在这40 min里,前35 min空压机空载,后5 min停机,接着空压机启机进入加载运行。这样就出现了为了一点节能效果而导致空压机反复启机(每90 min启动一次)。
此时有两种方式的选择,第一就是按照工况1的原则,增加空车过久的设置时间,使这40 min内空压机一直空载运行,处于加载-空载的运行循环。
另外一种就是缩短空车过久设置时间(从35 min调整为5 min),这样空压机运行时间可压缩至每天15 h (乌兰实测值),每天可节能30 kWX9 h=270 kW·h。此时节能效益初步显现,根据现场实际情况,可以认为节能收益大于每90 min空压机启动一次可能带来的设备损耗。
6.3 工况3:有2台压缩机处于冷备用状态(全部断电)
采用与工况2同样的参数设置策略,可实现空压机每天约运行8 h (乌兰实测值),每天仅空压机一处节能便可达到30 kW伊16 h=480 kW·h。
空压机作为增压站的主要耗能设备之一,存在巨大的节能降耗空间。对其运行参数的定期统计和分析,不仅为空压机的运行工况调整提供了决策依据,还为空压机的预防性维护保养提供支撑,达到节能降耗与安全可靠运行的平衡。
7 经验与启示
(1) 定期开展空压机系统相关参数的趋势分析。
定期对空压机重点参数尤其是总管网压力和水露点进行历史数据分析,便于及时发现空压机运行中存在的问题,为机组参数设置和预防性维护保养计划提供决策依据。
(2) 统计空压机运行时间和加载时间。交接班记录中仅统计了空压机运行时间,未统计加载时间。在乌兰发现上述问题后,让羊肠子沟站统计了加载时间后发现,3#空压机也存在问题,即8月30日运行9 h,加载9 h,31日运行15 h,加载15 h。
7.空压机的余热回收
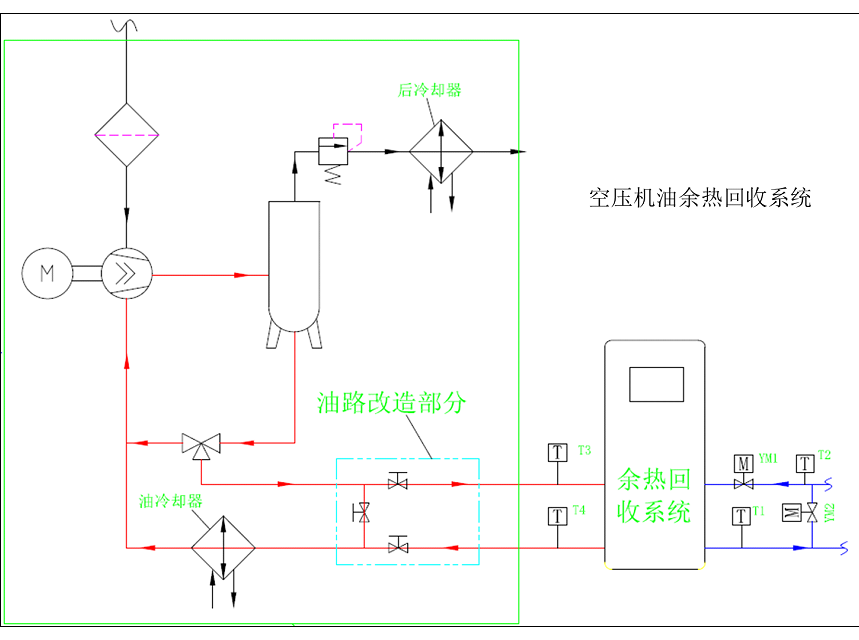
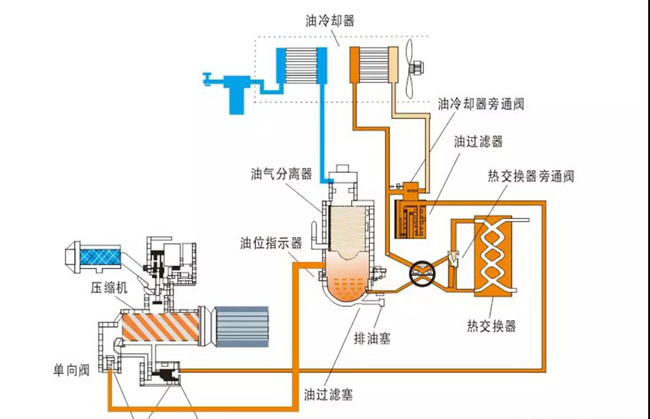
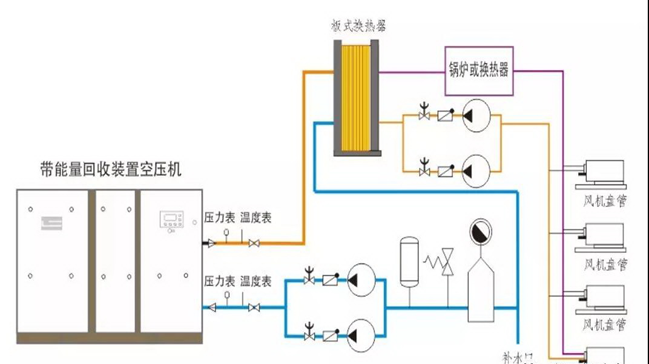
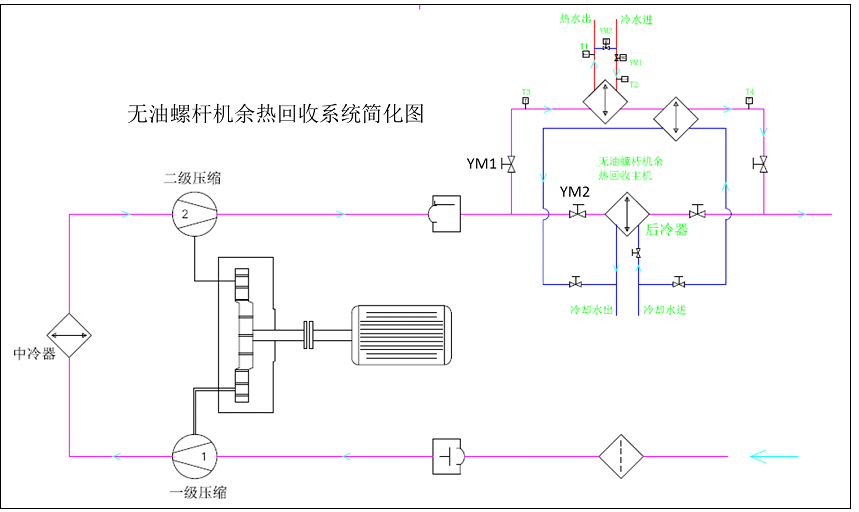
主机安装就位前,画好横向中心线位置,并在相应位置做好标记点; 空压机余热回收系统主机预留检修位置; 支架底部应做好基础且安装到位,螺栓、螺母、垫片无缺少且紧固; 组装、安装和基础制作中所应用到的钢材应考虑防腐要求,未经处理的钢材应按设计要求进行清除焊渣、除锈、热镀锌、刷防腐漆、银粉漆等的处理。
管道按图纸进行分段制作,根据安装情况适时穿插吊入; 管路及配件按正确的方法联接,连接应做到连接牢固、密封可靠、密封填充物不得裸露在外面; 热工管道焊接采用手工钨极氩弧焊打底,手工电弧焊盖面,其他钢管焊接均采用电焊; 管道按施工图中标注尺寸安装,要求横平竖直,有坡度要求的,按设计要求施工,各项允许偏差均要符合施工验收规范规定; 管路安装应按设计要求对管路增加支撑及固定,其支撑用的支架应有足够的强度和刚度,起到支撑管道重量、防止管道下垂弯曲的作用; 在系统管路通过混凝土板和墙壁时,要结合设计要求及房屋结构,合理安排管路,正确选择穿墙位置,并加装穿墙套管; 按设计要求,阀门应安装在容易操作的地方。阀门运转灵活、关闭严紧、达到设计要求,其它各种管件无损坏泄漏现象; 所有的管道要有标示标签,阀门要有标示牌; 管道和阀门在安装后,需进行强度和严密性试验,强度试验压力按公称压力的1.5倍进行,严密性试验按公称压力进行,试验时间分别为5分钟,严密性试验不合格的阀门不得使用; 管道试压合格后,需对管道冲洗和吹扫。 施工安装过程中应复核冷、热水管的压力等级和使用场所,冷、热水管不得混淆。管道标记应面向外侧,以便于查找, 容易发生故障的设备及附件两端采用法兰式或者活接头连接,以便维修更换。 电磁阀、过滤网等配件及设备严格按厂家推荐方式或设计要求安装。其中电磁阀两端按设计要求安装旁路管道及手动阀,当其发生故障时用手动阀工作。 系统管道需要安装吸排气阀等保护装置及集热器要设有一定的维修阀门。
保温材料及保温层厚度达到设计要求及使用要求。 防腐前,钢材表面进行除锈处理,除锈合格后的钢材表面在8小时内涂装底漆,以免发生二次生锈。 配制的涂料要涂刷均匀,不得漏涂;底漆表干后,即可涂面漆。 管道保温在管道压力试验结束后进行,保温材料与管道及设备、配件贴合紧密,接缝处采取避免热损失措施; 保温层连接牢固,外部使用铝皮防护,接缝处朝下,外防护层表面应光洁平整、无裂纹、无划伤、无飞边,应尽量的减少接缝数量; 所有需保温的设备及配件均做好保温处理;
电气的外部接线应按线端头标志进行,接线应排列整齐,清晰、美观,导线绝缘应良好、无损伤; 控制系统中电源出入线应符合要求,所有线的接头应连接可靠、牢固,并做好绝缘处理; 泵的进出水端应加手动阀,以便于进行流量调节; 自动控制箱要求包含漏电开关、时间控制、温度控制器、交流接触器、过载继电器等相关保护装置。 控制电柜要求符合接线规范,有清晰的线标及相关线路接线图纸。 控制电柜要求可靠接地,能够很好的防水和通风散热。 温度传感器的定位和安装与被测部位有良好的热接触,温度传感器进行良好的保温。 接驳的阀门与原有的阀门能够进行正常的联动, 自动控制箱要定温,定时,定水位全自动控制,且备有手动控制功能。
管道的耐压试验,
按要求对管道充水进行打压试验,各处没有渗漏为止。 设备、配件等辅助设施的运行检查。 水泵运转是否正常,是否泄漏 电磁阀在开关过程中声音是否正常,是否泄漏。 止回阀工作是否正常,是否泄漏。 排气阀排气是否正常,有无液体溢出。 各种手动阀门运转是否灵活,关闭是否严紧,能否达到设计要求,其它各种管件是否有损坏泄漏现象。 若系统中有压力表和流量计,检查压力及流量是否在正常的范围内。
保温层检验:检查所有部位的保温,保温层不能有浸湿和破损现象。 控制系统的检验:控制系统中所有温度及液位的显示是否正常。控制系统中所有的自动控制及手动控制在系统应用中是否正常。控制系统中所有的保护功能是否能正常工作。
8.空压机节能效果计算方法!
一、耗能分析
螺杆压缩机的运行原理决定了压缩机的能耗,当压缩机的产气量大于用气量时压缩机会卸载,当设备用气量大于产气量时压缩机会加载,这样不停加卸载造成管网压力很不稳定,电流波动也比较大。
二、节能空间分析
1、压缩机卸载时压缩机做的全部是无用功。
2、当压缩机加载时上升的压力也是不必要的,因为加载压力设定就是你的最低需求压力。
三、能耗计算方法
1、卸载能耗约占压缩机功率的52% (可以测电流得到精确数据)220A/ 420A= 52% (压缩机功率满载约250kW) ,卸载功率=250×52% = 130kW ,加载功率250kW 。
2、KP 压力上升1KG ,能耗约占整个系统的7%。
3.压力设定在5.7-7.0公斤之间,把空压机的进气门一直打开,空压机理论上是出于一直加载状态。
4、统计期间共230小时的运行记录,空压机的平均加载率是57.7%,平均卸载率42.3%,空压机月平均运行时间700小时。
5、一月节约计算:
月卸载时做无用功=卸载功率×卸载率×运行时间=130kW×42.3%×700=38493度
月加载时升高1公斤压力耗电量=加载功率×加载率×运行时间×KP=250×57.7%×700×7%=7068.2度=7068度
月总节电量=月卸载时做无用功+月加载时升高1公斤压力耗电量=38493+7068=45561度
但是压缩机改造变频后不能完全的消除卸载,因为螺杆压缩机在变频到25HZ 后再不能再降低转速,降低后效率急速下降,所以卸载的20%能耗不能节约,这样每月总节约为=45561×80%=36449度电
用电记录:空压机每月耗电量为158760度
节电率=36449/158760=23%
9.空压机余热回收2
一、前言
空压机、冷冻机耗电量占全国用电量的35%,其中空压机用电量至少占25%。在工矿企业耗电量较大的往往是空压机,并且经常占到了全厂用电量的50%,尤其在国内空压机使用效率普遍较低。我们知道空压机在运行时要产生大量的热量,风冷机组要把热量排入大气中;水冷机组要通过冷却塔把热量排入大气中。
根据美国能源署统计:压缩机在运行时,真正用于增加空气势能所消耗的电能,在总耗电量中只占很小的一部分15%,大约85%的电能转化为热量,通过风冷或者水冷的方式排放到空气中。
放任这些“多余”热量排放到空气中,既影响了环境,制造了“热”污染,而且现在的生产型企业,求热若渴,看着不得不放弃掉的热能,怎能不心疼?
其实对于这些被浪费的热量,我们大可不必“望热兴叹”,采用空压机热能回收技术,这些看似多余的热量,其中有50%是可以被回收利用的!
二、为什么要回收空压机余热?
由以上图表我们不难看出,空压机在工作的时候,真正用于增加空气势能所消耗的电能在总耗电量中只占很小的一部分,约20%左右。约80%的耗电转化为热量,通过风冷或者水冷的方式排放到空气中去。
根据流体力学,空气在压缩过程中分子的势能的转化将产生大量的热能,压缩机的热量如果不排放,将影响空压机的正常工作,影响压缩空气的质量。当然这些热量如果排放即浪费了大量的热能(可惜)又加剧大气“温室效应”,造成热污染(可恶)。
我们现在算笔帐:
以160KW空压机为例:
用于压缩空气的消耗的电能
160×20%=32kW
转化余热浪费的电能
160×80%=128kW
那么转化为余热为:
1小时浪费热量 11万大卡
1天24小时浪费热量 264万大卡
1年360天浪费热量 95,040万大卡
针对空压机配套热回收系统大约可以回收余热的50%左右,即占空压机轴功率的40%。则160kW空压机每年可回收热量95,040×50%=47,520万大卡
相当于每年:
节省0#柴油 46吨
节省天然气 52,800立方
节省用 电 55.3万度
节省标准煤 67.9吨
随着能源价格的进一步增长,回收空压机余热的经济效益越发明显:经不完全统计,采用空压机余热回收技术后,参照2016.7.1的燃油价格,按空压机轴功率计算,平均1kW的轴功率每年大约可以节省2,100元RMB。
这说明,提高空压机使用效率的潜力很大,节能空间巨大。
三、空压机余热回收应用范围:
1、最为常见的是制取热水,用于洗澡等,如铸造、冶金和矿物开采等工作环境相对较差的行业,可将回收的空压机余热加热自来水到50至60℃,供工人洗澡使用。尤其厂矿企业独立配置锅炉供热的,可以为锅炉提前预热,或单独使用空压机余热回收直接供热,这不仅降低了能耗成本,而且避免了对环境的污染。
2、反渗透纯水制取用热:食品饮料、半导体和医药化学等行业在生产过程中,往往用到大量的反渗透纯水。纯水需要在25℃的特定温度下制取,当春季、秋季和冬季水的温度低于25℃时,必须投入设备、消耗燃料为水升温。回收空压机的余热用来生产纯水,不但可以减少燃料的消耗,甚至可以减少加热设备的投入成本。
3、采暖用热:在长江流域及北方地区,冬季需要供热采暖,而这部分热量往往是利用锅炉加热提供的。现回收空压机的余热用于采暖,不但节省了能源的消耗,还可以减少锅炉的装机容量,进一步降低设备上的投资。
空压机余热回收是一项非常环保的节能方式,也是目前备受推崇的节能方式。空压机余热回收是将空压机的高温油经过热交换等技术处理把热量传递到冷水中,冷水被加热后流到保温贮水桶中,这样就可达到热能回收的目的。
四、余热回收经济效益
目前,大多数空压机企业用户,开始回收利用空压机热量,将空压机热量转为热水,供应工厂所需用热点,停用原有冷却系统,减少热能浪费和成本投入。回收余热,可将能源利用率提高到85%以上,可在5~8个月回收成本;
螺杆喷油式空压机余热回收原理
喷油螺杆空压机,以油气双回收为主,先由冷水增压后经过换热器和主机,把油、气温度降到45℃左右,产出热水可预先设计控制在50℃~80℃。热水远距离输送进入储水箱,满足工厂生活用水、工艺用水。
离心式空压机余热回收原理
无油螺杆式空压机余热回收原理
无油螺杆、离心式空压机,以压缩空气热量回收为主。为保证压缩空气洁净度,回收末级压缩空气热量,结合原冷却系统,冷水增压先吸收冷却水热量,预热后再进入主机,同样把压缩空气降到40℃左右,产出热水可设计控制在50℃~80℃。
五、举例说明:
轴功率×回收率×加载率×热量转换=可回收热量
一台37kw有油螺杆机,可满足多少人洗澡用水?
轴功率:37kw/h
回收率:75%(油气双回收效率)
加载率:85%
热量转换:860kcal/kw
可回收热量:37kw×75%×85%×860kcal=20285.25(kcal/h)
产水温差:45℃
产水量:20285.25kcal/÷45℃÷1000kg×24h≈10.8(T/天)
人均用水量:40L/天
热水可供人数:10.8T÷40L≈270(人)
因此一台37KW空压机,如果24小时开机,将可供企业270人员工用热水洗澡。
如果是75KW,将可供不少于 500名员工用热水。
而运行能耗只是增加了一台0.7KW的水泵能耗。
回收空压机热量,免费热水供应,帮助企业合理利用能源,减少不必要的热能浪费,给企业带来持续节能经济效益。
六、余热回收工程示意图
七、适用场所
*热效率高,主要用于空压机常开之单位。
*工厂等企事业单位生活用热水。
*工业生产用热水及中央供暖场所。
*几十人到几万人,几吨到几百吨热水均可使用。
9.空压机节能改造案例两则
空压系统电能消耗占工业能耗的8~10%左右,全国空压机耗电量约为2260亿kWh/a,其中有效能耗只占66%,其余34%的能量(约768.4亿kWh/a)被白白浪费掉,空压系统的节能亟待高效开展。大量的数据表明,压缩空气系统的主要费用都耗费在运行环节上,在其生命周期中,运行费用(电费)占据的比例高达78~92%。
如水泥生产是高耗能行业,水泥行业能耗占全球能源消耗的2%,水泥行业的二氧化碳排放量占全球碳排量的 5%,而全球超过50%的水泥在中国生产。水泥工厂最大的挑战是能源消耗(热能和电能消耗),约占生产成本的 50%~70%。
近年来,中央和地方政府对能源密集型的水泥行业加强管控,要求提高生态效益和可持续性,并出台规章制度和罚款条例,敦促水泥企业降低能源消耗,减少二氧化碳的排放。因此,如何通过精细化管理,对水泥能耗深入挖潜,提高能源使用效率,是每个水泥企业都要面临的一个课题。
根据现场调研与检测获取的大量生产数据(表1),结合工程经验,发现大部分压缩空气系统运行能耗高的主要原因如下:
几年前配置的空压机大多属于低能效设备(表2),与终端等设备匹配不合理,仅仅为了满足生产的基本需求;空压机调节方式落后、无集中控制,用气量随机变化时,空压机因卸载而浪费严重;末端设备用气不合理、效率低、设备用气存在浪费。
没有对供气压力进行分级规划,而是简单采用高压供气外加机械自力式减压阀来满足不同的压力需求,大量的能源浪费在阀门上。此外,当需求侧用气量变化引起管网压力的随机波动,为了避免机组的频繁启停,需要设定一个很宽的压力变化范围,造成空压机出口压力的大幅波动,增加了空压系统的运行能耗。
1、空载能耗高。目前企业压缩机为单台N立方,压缩机开停只有N或N的倍数,空压机设备开停依赖人工管理的传统。尤其在用气负载频繁变化时,系统不能快速反应,也不能实现压缩机排量的微调。这形成了空压站各压缩机的空载。
通常情况下,当压力达到y公斤时,空压机进入卸载运行状态,当压力降到x公斤时,压缩机进入空载状态,即关闭进气阀使电机处于空转状态,同时将油器预分离罐中多余的压缩空气通过放空阀放空。关闭进气阀使电机空转虽然可以使空压机不需要再压缩气体作功,但空压机在空转中还是要带动螺杆或者活塞做回转运动,电耗仍在继续发生。实际检测发现,空压机空载时的能耗高达其满载运行时的40%~55%(请参考表3)。
2、爬升能耗高。螺杆压缩机有两种运行模式,加、卸载运行模式或空载、满载运行模式。加、卸载控制方式使得压缩气体的压力在x公斤~y公斤之间来回运动。x公斤是最低工作压力值,即能够保证用户正常工作的最低压力(加载压力)。一般情况下,x公斤、y公斤之间关系可以用下式来表示:y公斤=x公斤+(1+δ),δ是一个百分数,其数值大致在10%~25%之间。压差一般在一公斤以上。
通过理论计算和实际检测,得知空压机压力每增加1公斤,能耗增加5-6%。由此可知,在加、卸载供气控制方式下的空压机,其工作气压由x到y,有一个气压爬升的能耗,存在事实上的能源浪费。同时,高于x公斤的气体在进入用气终端前,其压力需要经过减压阀减压至接近x公斤,压力越高流速越快,这就造成同样的工况,压力越高所耗气量越大。这一过程同样是一个能源浪费的过程。
3、传统管理。在空压站的使用管理过程中,存在两种不可避免的矛盾。一种是企业对空压机管理人员有明确的考核,那么会出现气压经常不够或能少开就少开的习惯,不利于生产线的正常运行,或出现压力达不到设备使用要求导致用气终端故障增加。
另一种是对空压机管理人员没有明确的考核,这就会导致空压机多开、空压站空载能耗高的结果。无论哪种管理模式,其结果都会是空压站电能浪费增大,而且不利于安全生产。
案例一:
某水泥有限公司4500t/d熟料生产线项目于2008年8月18日点火投产,总投资6.2亿元,年产熟料155万吨,水泥200万吨,建设范围自石灰石、砂岩矿山开采及破碎至水泥成品出厂,并同步配套建设纯低温余热发电系统,属典型的节能型项目,污染物的排放优于国家规定的标准,可以有效的提高现有资源的综合利用率。
下面是就该公司采用《合同能源服务管理》方式对现役高危、高耗能空压机产品实现节能改造的节能效益和工程项目达成方式的阐述,请参阅:
1、改造前服役空气压缩机能耗数据见表4。
2、改造后服役空气压缩机能耗数据(表5)
(1)该司正常使用是5台,铭牌功率110/kW*5=578kW;实际耗电557kW/每小时(实际运行压力在0.63MPa);理论排气量100.6m3/min,实际排气量在85.51m3/min;
(2)表2中得出:采用笔者公司更节能的永磁同步双级压缩永磁变频一体机5台,90/kW*5=450kW;实际耗电在453kW/每小时,理论排气量99m3/min,实际排气量在90m3/min;
(3)空压机设备节能改造前后节能量数据:采用同压力、同排量的节能空压机替换现用的空压机完成等同的生产量,比原来的空压机在加载运行状态下每小时节省电量约104度,每小时节省电费约72.8元(电费按0.7元/度计算)。
结论:空压机节能改造后
A、用户节能效益收益
①运行1小时可节约电量约104度;可节约电费约72.8元;
②运行一年(365*0.95=346.75天/8322H)节约电量86.5万度;可节约电费约60.5万元;
③运行4万小时可节约电量约416万度;可节约电费约291万元。
用户节能效益收益,见表6。
B、社会节能效益
①运行1小时可节约标准煤约0.0332吨;可减少二氧化碳排量约0.0664吨;
②运行4万小时可节约标准煤约1331吨;可减少二氧化碳排量约2662吨;
随着碳排放上网交易,截止2019年7个试点省市的3000多家重点用能企业已加入,各地平均成交价30元左右。
案例二:
某玻璃股份有限公司,占地800余亩,员工800多名,公司注册资本2亿元人民币。公司建于2004年,拥有两条700t/d超白玻璃及深加工生产线,年产超白玻璃860万重箱,钢化玻璃50万平方米,中控玻璃280万平方米。
下面是就该公司采用《合同能源服务管理》方式对现役高危、高耗能空压机产品实现节能改造的节能效益和工程项目达成方式的阐述,请参阅:
1、改造前服役空气压缩机能耗数据见表7。
2、改造后服役空气压缩机能耗数据见表8。
(1)该司正常使用是3台,铭牌功率250/kW*3=750kW;实际耗电846kW/每小时排气量120.8m3/min;
(2)采用笔者公司更加节能的永磁同步双级压缩空压机3台,200/kW*3=600kW; 实际耗电在660kW/每小时,排气量120.81m3/min。
(3)空压机设备节能改造前后节能量数据:采用同排量、同压力的节能型空压机替换现用的空压机完成等同的生产量,比原来的空压机在加载运行状态下每小时节省电量约186度,每小时节省电费约117.1元(电费按0.63元/度计算)。
结论:用户空压机节能改造后
A、用户节能效益收益
①运行1小时可节约电量约186度;可节约电费约117.1元;
②运行一年(365*0.95=346.75天/8322H)节约电量约154.7万度;可节约电费约97万元;
③运行4万小时可节约电量约744万度;可节约电费约468万元。
用户节能效益收益见表9。
B、社会节能效益
①运行1小时可节约标准煤约0.0691吨;可减少二氧化碳排量约0.1382吨;
②运行4万小时可节约标准煤约2764.8吨;可减少二氧化碳排量约5529.6吨;
③随着碳排放上网交易,截止2019年7个试点省市的3000多家重点用能企业已加入,各地平均成交价30元左右。
节能实现的方法
1、使用现有的变频控制柜将其改造:
在原有的空压机基础之上增加变频控制柜从而达到节能减排的方法。
2、节能置换为变频空压机(更换新机)
根据当前的空压机折旧进行回收,提供全新变频机组从而达到机组节能减排的标准。
3、节能计算,用气量跟空压机排气量更换机型(工频机)
根据当前的空压机产气量及贵司的用气量进行换算,更替比原来小的机型,但是满足当前生产使用的机型从而达到节能减排的标准。
案例展示
上海某单位,所使用型号的机器为M132-A8机组,功率为132KW。.排气压力都为0.85 Mpa。
M132-A8机组节能分析:
空压机的加卸载是空压机运行工况的一种重要性能,加载时间和卸载时间是空压机运行的重要参数。变频改造后消除了系统的加卸载时间,从而节约电能。
贵公司现有的空压机的规格是:功率为132KW、排气压力为8.5 bar(一般情况),加载率约为 18.7%,使用时间为3600小时/年
A:非变频空压机
重车消耗(132KW*18.7%实际用量)+空车功耗(132KW*52%空车损耗功率*48%的零供气待机时间)=57.631 KW/小时X8640h/年X1元/度=497931.84元/年
B:采用变频节能柜的空压机 132KW*93%(恒压供气降低了7 %的功耗)*18.7%实际用量=22.956KW/小时X8640h/年*1元/度=198339.84元/年
实际节能=497931.84-198339.84=299592元/年
考虑到变频器的功耗=132X3%X8640小时X1元/度=34214.4元/年
实际节能299592元-变频器功耗34214.4元=265377.6元/年
最终节能为265377.6元/年。
M132-A8机组节电率为53 %。使用变频节能柜预计5个月收回成本,变频柜本身使用年限为10年,可以节省更多能耗。从而达到节能环保等目的。
根据数据所计算,年约节省26.5万元。数据大概有所偏差20万元是可以节省,案例当中空压机运行时间为3600小时,很多企业运行的时间为24小时不间断运行,那将有更多的节省空间,企业运营成本将大大降低。